Cable infill, or “cable rails,” as they are commonly known, work well for both indoor and outdoor railing systems. They can easily be mounted to almost any post style or mounting configuration (top mount, side mount, core drill, etc.). Cables are a popular component of railing systems because they are thin, flexible, and yet very strong. In fact, stainless steel cables can usually withstand 1,000 to 3,000 pounds of force without breaking. Cable infill can provide a sleek and modern look, and can appear practically invisible from a distance, providing a nearly unobstructed view of the surroundings. This is why cable railings have become so common on decks where the view is striking (like around the ocean, mountains, lakes, etc.). Cable railing also looks great indoors, as it can tastefully define spaces, while maintaining a feeling of openness within the living areas.
Like all infill components, cables are subject to building code requirements. There are minimum loads to be resisted and maximum openings to be heeded. The load requirement is a 50-pound horizontal force applied on a 12-inch square area. The opening size is governed by a 4-inch sphere. What often happens is that both of these provisions are combined to where the specification documents or the inspectors refer to a 4-inch sphere being pushed by a 50-pound force. The fact of the matter is that the 4-inch sphere is intended to be a measuring device, not a load-delivering implement. Nowhere does the code mention the two requirements acting together.
Glass infill provides a railing system with a clean, transparent look that is ideal for situations where added safety is required. Tempered safety glass is frequently used, providing a strong, safe infill that protects building occupants from accidental injury, while delivering a classic look for the railing design. An added benefit of glass infill is that it also serves as a wind barrier, which can be useful for outdoor decks in coastal areas or on the upper levels of buildings, where winds tend to be strong.
Bar rails are another classic railing infill look. Bars may be square or cylindrical, providing a strong, secure infill for the railing system with an aesthetic appearance that highlights its strength. As a safety feature, railings with horizontal or vertical bars can prevent accidents or serious injury by providing a secure barrier as part of the railing system. Bar rails have traditionally required on-site fabrication and welding, which limited the aesthetic element because the welds could be difficult to “finish” on-site. New technologies now provide prefabricated systems that architects and building professionals can design ahead of time and have custom made at a fabrication facility. These component-based systems remove the need for the extensive on-site construction and welding, and they come perfectly “finished” and ready to be installed.
Understanding Stainless Steel in Ornamental Railing Systems
There are several considerations to keep in mind when selecting the material type for a railing project. First, stainless steel is stronger than aluminum. Tensile strength is measured as force per unit area, and in the International System of Units (SI), the unit is the “pascal” (Pa); a multiple is called “megapascal,” or MPa. The ultimate strength for stainless steel is 590 MPa versus that of 300 MPa for 6061-T6 aluminum. Moreover, the surface hardness of stainless steel is much higher than that of aluminum, and thus it resists scratches and is easier to maintain than its aluminum counterparts. Additionally, stainless steel’s fatigue performance is twice that of aluminum, and that adds to a product’s durability. In terms of railings, a stainless steel rail will likely provide many more years of safe, aesthetically appealing use than an aluminum system.
The benefits of stainless steel’s additional strength are evidenced in the railing system’s posts and handrails, which can be constructed to be much thinner than those made of aluminum. A “strength-equivalent” stainless post is 50 percent thinner than an aluminum post.
Stainless steel is 100 percent recyclable, making it a material of choice for architects who design with sustainability in mind.
Appearance is also a key advantage of stainless steel. No other commonly used railing material can match the ease of maintenance and stunning good looks of stainless steel. This is one of the reasons you will find it used frequently on luxury appliances like high-end gas ranges and refrigerators.
Different Types and Grades of Stainless Steel (304, 316)
Stainless steel is usually divided into five categories: ferritic, martensitic, duplex, precipitation hardening, and austenitic, the most commonly used stainless. Austenitic stainless steel comes in many different grades, used for different purposes, with the two most common grades for architectural applications being Type 304 and Type 316.
Type 304 stainless steel is the most common grade, also known as A2 stainless steel or “18/8 stainless steel” (18 percent chromium and 8 percent nickel, which are the main non-iron constituents). This grade of steel is a popular choice for building materials, machinery parts, and food-handling equipment because it has low electrical and thermal conductivity, and it resists corrosion remarkably well. Because of these traits, Type 304 is a popular choice of material for indoor and outdoor railings.
While Type 304 stainless steel is highly resistant to corrosion (both environmental and corrosive media), it is susceptible to pitting and crevice corrosion in warm environments when exposed to chlorides, namely marine environments. It is also susceptive to stress corrosion, cracking at high temperatures (above 140 degrees Fahrenheit, or 60 degrees Celsius).
Type 316 stainless steel, otherwise known as “marine-grade stainless,” is the second most common austenitic stainless steel. Higher nickel content (10 to 14 percent) and the addition of molybdenum increase this grade’s resistance to corrosion. Like Type 304, this type of stainless steel has a low conductivity of electricity and heat, and so it is appropriate for a wide range of uses. Unlike Type 304, this type of stainless steel resists pitting corrosion very well, making it desirable in exterior and even coastal environments.
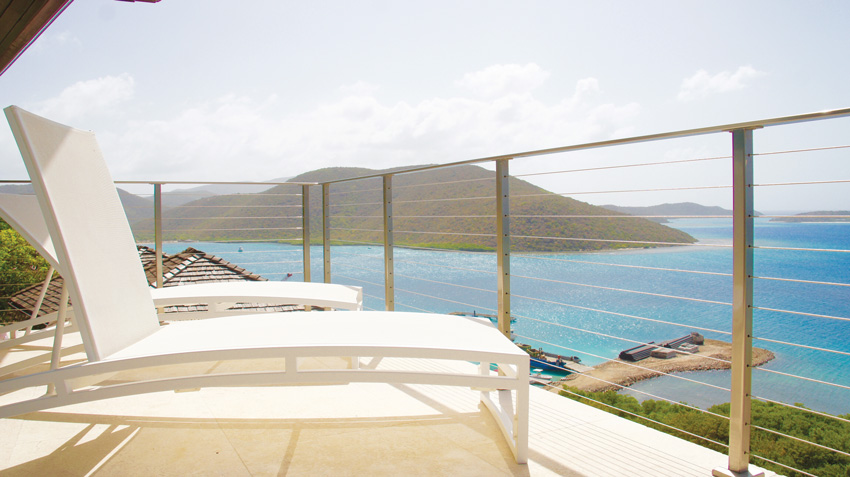
Stainless steel is one of the most forgiving materials, resists corrosion, and is very easy to maintain. The ultra-thin cabling also allows the surrounding natural beauty to be highlighted with minimal distraction, yet the quality craftsmanship and fine detailing are just as breathtaking when in focus.